某企业有A和B两种产品。产品A的制造主要以装配过程为主,工序较简单,而且属于单件小批量的制造。产品B是一个由五阶段构成的生产存储系统。
由于企业面临的竞争日益激烈,要求企业必须进一步加强对生产成本的控制,不仅要保证准时向用户供货,而且要最大程度地降低库存,减少积压。运用MRP不能产生一个可行的车间作业安排表,而计划定单的发放和接收仅仅规定了定单的起始时间和完成时间。MRP不能确定每一作业的准确的加工时间及加工地点。当一项任务下达到生产车间时,并不能保证在计划提前内完成产品的加工。因此,这是一个很不精确的用于控制车间作业安排、确保满足交货期目标的工具。
公司为改变现状,成立了项目小组。项目小组通过反复研讨,认为生产运作方而的问题主要是由于没有采用一个先进适用的生产管理方式所造的。项目组对生产运作管理的理论进行了研讨,借鉴了国内外企业运用JIT、MRPII的实际经验,提出了公司应用MRPII与JIT混合控制系统、改善生产与运作系统的总体思路。采用MRPII理论和方法来进行生产计划地制定工作,采用JIT的原理和方法来开展生产控制工作,特别是生产现场管理工作,在瓶颈环节的前道工序设置一定的缓冲库存,以此工序为节点,前边工序一种看板为工具实行拉式生产,后边工序实行推式生产。
一、生产中出现的问题
1、产能不够
2号加工中心从其他加工中心获取毛坯,11日时已经有100个工时发出但积压未完成的在制品量。从表1中可以看出,这一周虽然其实际投入量略高于计划投入量,但实际产出量却持续地低于计划产出量,说明该加工中心受到了生产能力的限制,需要采取加班等措施来解决产能问题。
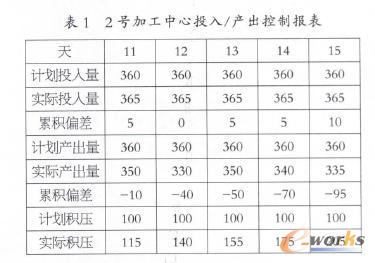
2、原材料投入不足
3号加工中心从其他加工中心获取毛坯,20日时已经有50个工时发出但积压未完成的在制品量。从表2中可以看出,投入量和产出量的偏差均在增加,说明该加工中心缺少必要的毛坯而不是生产能力不足,需要增加其领料看板。
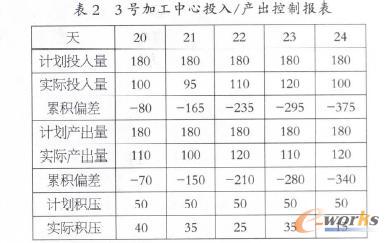
二、单阶段定量在制品法改造
产品A的制造主要以装配过程为主,工序较简单,属于单件小批量的制造,因此可以考虑采用一种看板控制的替代方法——CONWIP定量在制品方法。此方法是在装配线的初始阶段投入看板,看板流通于整个装配过程,直到成品发运后看板才回到初始阶段。这样,通过控制看板的总数可控制在制品的总量,根据客户的短期需求及瓶颈资源的情况来调整看板数目,就可实现能力平衡。
从机理上看,在整个生产线上使用看板的Pull方式,但是后续工序靠投入的看板来推动系统运动,属于Push方式。
三、多阶段混合控制策略
MRPⅡ与JIT是在不同环境中产生的,二者各有优缺点,对于我国的制造业而言,无论生搬硬套哪一种方法都是不适宜的。只有根据我国国情,将二者有机地结合起来,发展适合国情的Push/Pull混合控制策略才是正确的。
四、MPR/JIT混合控制方法的设计
1、控制层的两大决策
(1)制定月生产计划。月生产计划对应于MRP中的生产计划大纲,是生成主生产计划的依据。具体计算月产量的公式如下:月产量=月要货量+成品安全库存-当时成品库存。
此外,必须考虑对应的原材料库存量和生产能力(作粗能力平衡)是否满足要求,是否需要加以调整。
在定期系统下,根据客户需求率的变化,来改变成品的计划产量,所以成品的计划产量是不固定的。成品仓库的安全库存是用来预防在一个月内需求量、生产量的某些不可预测的波动。实际上,作为数据来源的客户月要货订单上的数据绝对准确,并且生产线可确保无异常情况发生,加上厂际看板的实施,成品仓库的安全库存可以压缩到很小的数量。
(2)从月生产计划分解周装配计划。周装配计划对应于MRP中的主生产计划,是确定整个生产的进度。周装配计划与月生产计划的最大区别是,必须考虑到在一个月内生产不同型号产品时生产能力的细平衡。与产品A相比,产品B的工装不同,更换装夹时间较长,机加工能力相对薄弱,电镀要求有一定的批量,所以在执行月生产计划时,必然存在着一定程度的需求与制造能力之间的不平衡。
对于以产品A为代表的单阶段定量在制品法,由于不存在上述问题,因此周装配计划只需根据客户的发货时间要求按反时间方向倒排即可。
对于产品B,如果同样按周为单位倒排,当能力不平衡时,解决的办法不外乎提前生产或拖期交货。提前生产要占用流动资金,增加存储费用,从而提高了产品成本;交货拖期则可能引起客户的抱怨。如果能给出符合实际情况的上述两种情况下的惩罚成本,运用运筹学方法可以得到惩罚总额最小的周装配计划,其思路如下。设该企业在计划期2006年3月生产产品A和产品B,每种产品要经过s台设备(s台设备是两种产品加工设备的并集)。根据客户月要货订单以及要货时间表,这两种产品每周的要货量为H1(t)和H2(t)。已知第m种产品对第n台设备的能力的单位需求量为Wmn(Wmn=0表示第m种产品不通过第n台设备),第n台设备第t周的可用能力为bn(t)(假设夹具每周更换一次)。在初始时刻,产品m的储量为Mm,Mm<0表示初始的欠产量。Xm、Ym分别为产品m单位产品提前单位时间的惩罚成本和拖延单位时间的惩罚罚款,通常Ym>Xm。
设第m种产品的第t周的计划生产量为Pm(t),则第m种产品第t周的超产量和欠产量分别为:
Pe=[Mm+Pm(k)-Hm(k)]+;P0=[Hm(k)-Pm(k)-Mm]+
其中,(X)+表示max{0,X}。
令总惩罚费用为F(P),假定一月四周,则周装配计划模型为:minF(P)=(XmPe+YmP0)
约束条件: pm(t)>=0m=1,2 t=1,2,3,4
WmnPm(t)≤bn(t) t=1,2,3,4
上述目标函数可转化为线性规划求解。经过权衡,认为目前可以简单地以周为单位按客户的发货时间,每班的生产定额等因素倒排编制周装配计划。
2、协调层的两大决策
(1)根据周装配计划分解日投料计划。根据MRP/JIT混合控制策略,生产的投料工序采用MRP控制,后续工序采用JIT的看板管理。按照MRP的方法,原材料的净需求量是周装配计划(主生产计划)和产品BOM表确定的毛需求量减去在线的在制品存储量所得到的值。根据一周的原材料净需求量制定日投料计划,日投料计划每周制定一次,可按照实际反馈的生产统计和在制品统计数据随时滚动修改。
(2)根据日投料计划计算工序看板数量。按看板控制方式,如果一个工序的附属存储器中有空看板,而其上游存储器中有原料,则该工序应安排生产。在各工序间设置看板的主要目的是,通过控制各工序的附属存储器的容量大小,以实现对各工序的生产能力的有效控制,达到平衡生产线各工序间生产能力的差异,降低在制品库存的目标。如果生产制造过程相对稳定,那么各工序的看板数量就会在固定的数值上下波动。
初始看板数的计算公式为:N=Pv×Pt(1+m)/n。式中,N——初始看板数,Pv——每日该零件的生产速率,Pt——初始看板数的循环周期,m——余量因子(0.1 Pv是按物料需求计划得到的每日该零件应有的生产速率,每日该零件数的需求量可从日投料计划中得到。Pv与设备的常规生产速率,极限生产速率相比较后,从而判断是否有足够的生产能力。如发现能力不足,进行设备负荷调节和人力补充。如果能力实在无法平衡,则可以调整产品的生产计划。余量因子m可由技术人员根据统计结果和经验来选择。
用JIT改进MRP的物流控制方法将需求和制造能力之间的不平衡所造成的影响降低到最底限度,较好的提高了系统的自适应性。在制定月计划和周计划方面,研究了在能力不平衡的情况下采用提前生产和拖延交货时罚款最小的线性规划计算方法,提出了在实际生产过程中原材料供货不足、产量不够的时候需要采取的措施。
本文作者:刘 立 来源:万方数据
CIO之家 www.ciozj.com 微信公众号:imciow
免责声明:本站转载此文章旨在分享信息,不代表对其内容的完全认同。文章来源已尽可能注明,若涉及版权问题,请及时与我们联系,我们将积极配合处理。同时,我们无法对文章内容的真实性、准确性及完整性进行完全保证,对于因文章内容而产生的任何后果,本账号不承担法律责任。转载仅出于传播目的,读者应自行对内容进行核实与判断。请谨慎参考文章信息,一切责任由读者自行承担。